Preventive Maintenance
- Home |
- Preventive Maintenance


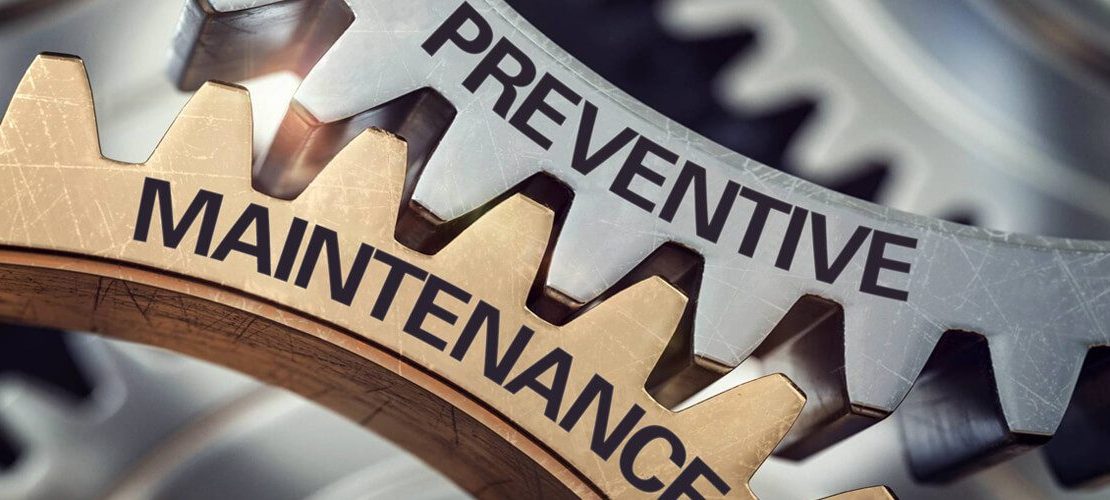
Another way to make production more efficient is to reduce unplanned stops and make planned stops. In unplanned stoppages; in case of a possible malfunction, the system will stop much more than it should, and productivity will decrease. Therefore, it is desired that the system should alarm before failure rather than alarming when it fails. Thus, with planned shutdowns, a motor informing “I will fail” before it fails will reduce the downtime by 80%.
Preventive maintenance may vary according to company priorities. It is possible to get this data by thinking in partnership with the maintenance team of the company and making a discovery.
- In general, the application is done as follows.
- The main points that will cause life-threatening problems if stopped are identified together with the maintenance team.
- Then it is discussed how to receive the signals,
- Alarms and lower and upper values for signals are entered into the SCADA or MES system.
- Mainly used Preventive Maintenance Data;
- To receive the vibration frequency of the engine with the engine vibration sensor and send a signal to maintenance if the vibration increases,
- If the current consumption of a machine or a motor increases through the energy analyzer, send a signal to maintenance without malfunctioning,
- Monitor the temperature of a mechanical shaft, part or motor with ultrasonic heat sensors and send a signal to maintenance if the temperature is above the set value,
- Communicating with Servo Motor or AC drives and sending a signal to maintenance in case of current draw,
- Entering the opening and closing life of pneumatic valves into the system and sending a signal to the maintenance team when they are close to the end of their life,
- Receiving signals from pressure sensors and sending a signal to the maintenance team when the system pressure drops below the desired value,
- Receiving signals from lubrication sensors and sending signals to the maintenance team when the oil value drops below the desired value.
Preventive maintenance signals can be sent to the maintenance team as e-mail, SMS or alarm to their systems. The maintenance personnel who go to the field for control at the beginning of the machine reads their card to the barcode and sends the information about when the intervention started by which maintenance personnel to the system together with the fault occurrence time.
This information can be transferred online to SAP and sent to HR, contributing to the generation of performance reports for maintenance personnel.