Data Collection and Integration from Production
- Home |
- Data Collection and Integration from Production


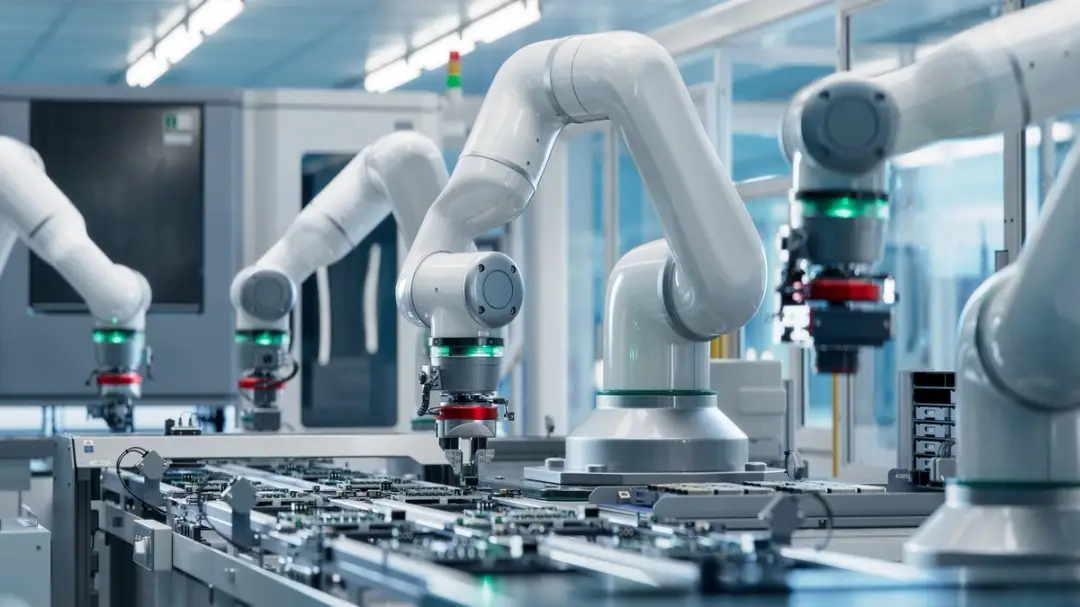
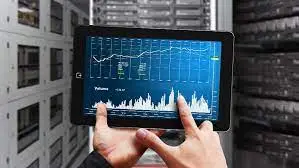
The most important element for productivity analysis, predictive maintenance process, etc. reports is to transmit online production data from machines, lines and robots to MES, SCADA or Reporting Software in a healthy and accurate manner. For productivity analysis and reporting, it is necessary to obtain the following data.
- Production Quantity
- Working Time
- Stopping Times
- Production Waste
- Energy Consumption
- In machines, even the type of product produced
- Alarms (For Maintenance)
- Raw Material Quantity
- Operator Information
Industry 4.0, Data Collection and Reporting (MES)
100 %Robotics Applications
100 %Industrial System Overhaul as Mechanics and Automation
100 %Installation of Automation Systems Including Mechanical
100 %To collect this data, it is first necessary to make an integration between machines. In other words, to make all the machines that are already producing to send data upstairs (MES) first. The basis here is to establish the Network we have established in the “IRP” and “IT” systems on the machines in production.
As Omni, when we receive such a request, we first make a reconnaissance in the field and analyze the situation. The data network we usually create is Ethernet/IP or Ethercat based. Since our company is the official system partner of Omron Elektronik in Industrial Automation, the hardware products we generally use (master PLC, Remote I/Os and HMIs) are Omron brands. Especially the quality of the Remote I/O units used in data collection from the field is very important in terms of receiving and sending the data to the MES.
It is very, very important that it is not affected by harmonics in the factory, does not interfere, is not affected by heat and humidity. In this regard, Omron is among the top companies in terms of quality.
As Omni, when we receive such a request, we first make an on-site survey and analyze the situation. The data network we usually create is Ethernet/IP or Ethercat based.
- We can send the desired production data to a database such as SQL etc. by converting the machines controlled by plc to Ethernet / IP with Ethernet / IP if there is Ethernet communication and Modbus RS485 if there is Modbus RS485, and then analyze them on a platform such as MES.
- If the system is very old, there is no communication port on the plc or if there is no plc, we can connect the signals to the Remote /IOs with Remote /IOs with Ethernet / IP or Ethercat communication ports and send them up (MES).
- If there is no sensor, we can get production quantity etc. data with additional sensors.
- For energy consumption; we can connect an energy analyzer to each machine or line and receive electricity consumption, water and gas consumption from flow meters and natural gas meters and send them to the control system for analysis and reporting.
- We can drop the work orders coming from the IRP system online on the HMI screens placed in front of the operators who follow the machines or lines, and we can follow the production by receiving the “arrow” start signal on the panel.
Ethics and Integrity
Ethics and honesty are very important concepts. We are committed to these two values to the end. We are responsible to our business partners, the companies we partner with and our employees.
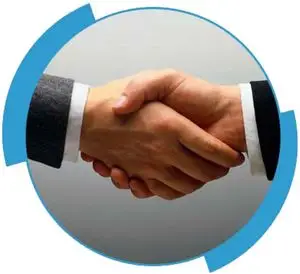
- Our References
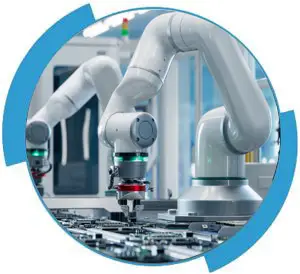
- Applications